Perfection in application is a must for consumer products: products targeted for the shelves need to be eye-catching to drive purchase. The client, a subcontractor specializing in the cosmetics industry and manufacturing for large multinational companies, was looking for a solution to apply labels with high-accuracy and without flaws such as air bubbles or ripples. In addition to accuracy, a second requirement was to align the labels precisely at a defined place on jars or cylindrical bottles.
The solution: System 1 Turning for wraparound labelling with orientation and cap reading
To achieve the goal, Etipack developed a custom system to apply a wrap-around label oriented with respect to the cap or other reference such as a brand or mark. To perform proper application, the system features a three-roller device that rotates the product and, through the integration of a custom vision system, applies the label while orienting it to the cap at the same time.
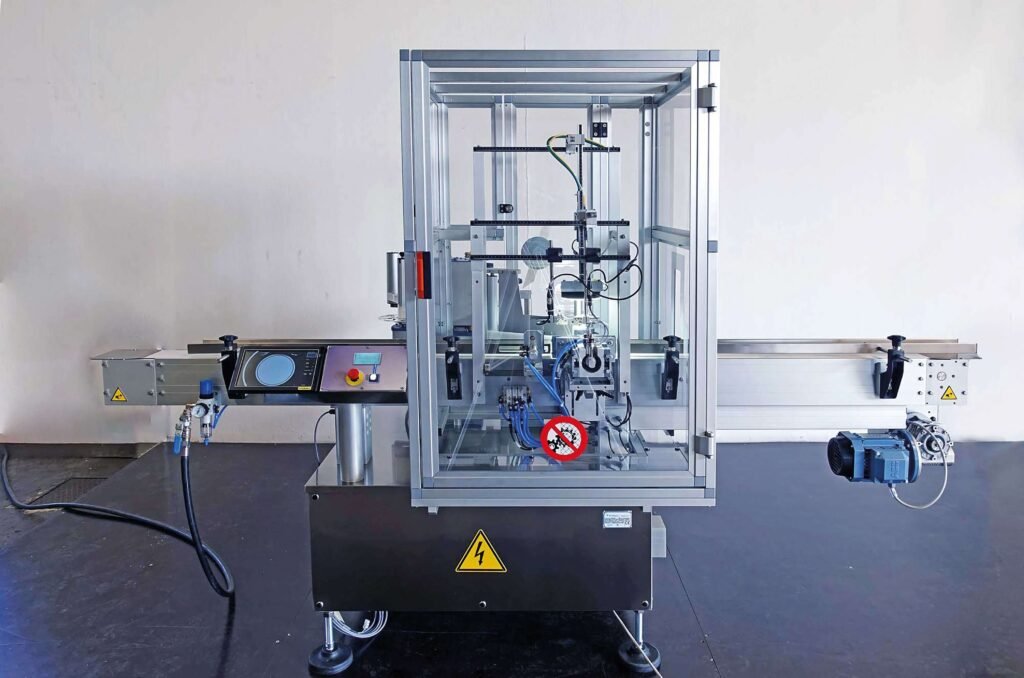

Customization and solution details to meet specific requirements
One of the special features of the machine is a special vision system with circular illuminator which is specifically designed to read the position of the cap or a defined point on each cylindrical product. Its purpose is to perfectly position the pressure-sensitive label so that it is oriented according to the jar cap.
To enable product rotation during labeling, the machine is equipped with a 3-roller opposed system: a large-diameter motorized roller and two opposed rollers connected to a pneumatic cylinder that capture the product and perform rotation.
An escapement system ensures the flow of products to be properly managed allowing the passage of the product to be labeled and holding the next ones in the queue for as long as it takes to perform both rotation and wrap-around application.
Product labelling is provided by an Energy 200 labelling machine. Equipped with retrofitted stepper motorization, it can reach a dispensing speed of up to 50 m/min. It features a capacitive sensor inside the reel to detect the ending of the backing paper.
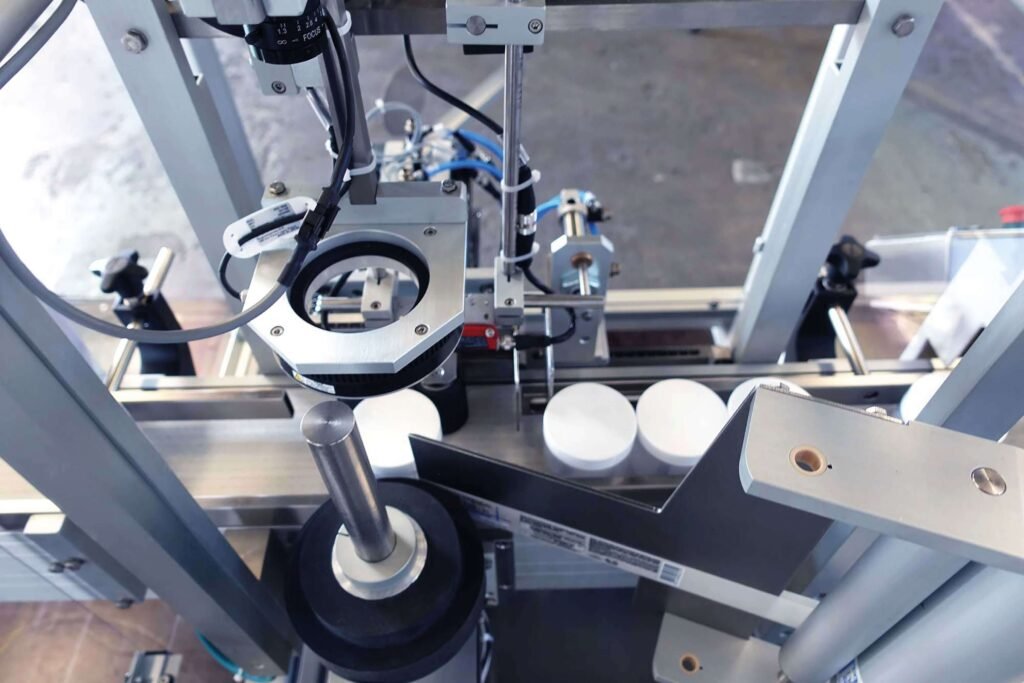

Results: precise and perfect wrap-around application for products in 3 sizes
The system allows the customer to manage wraparound labeling of 3 product formats with utmost flexibility and accuracy, solving processing problems that are common with cylindrical products such as defects like air bubbles and label orientation.
Products can be labeled at speeds of 45 pieces per minute in case of non-oriented products, and 25 pieces per minute in case of oriented products. Etipack offers a wide range of solutions to meet the multiple needs of the cosmetics industry.
Discover more etipack.it/en/settore/cosmetico/