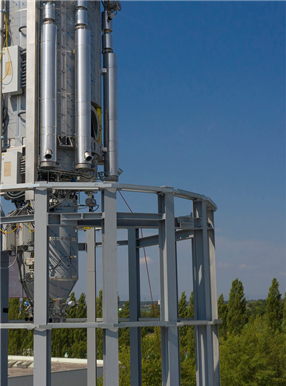
The Austrian recycling company installed another Starlinger bottle-to-bottle recycling system including SSP (solid state polycondensation) reactor at their production site in Müllendorf, Austria.
“It is also thanks to the new Starlinger pelletizing line that PET to PET is one of the most modern facilities in PET recycling worldwide. Since the foundation of the company we ensure that PET bottles in Austria are continuously recycled in a resource-saving way, contributing significantly to the circular economy in the country” comments PET to PET General Manager Christian Strasser on the capacity increase.
PET to PET Recycling Österreich GmbH recycled around 1.13 billion PET bottles (equals more than 28,200 tons of PET material) in 2020, also due to the newly installed capacities.
The company was able to increase throughput by 7.3 % despite the COVID-19 pandemic with subsequent lockdowns and the price decline for virgin PET resin.
The recoSTAR PET 165 HC iV+ bottle-to-bottle recycling system is the second line from Starlinger in operation at PET to PET. It has a throughput of 1,800 kg/h and achieves excellent decontamination results. The produced re-granulate can replace virgin PET at a rate of 100 %.
“The high quality of the recyclate is especially important to us. The Austrian beverage industry is continually increasing the share of recycled content in new PET packaging. Some of the producers even use bottles made of 100 % secondary raw material”, Christian Strasser explains.
Food-grade without compromise
The solid state polycondensation in the viscoSTAR 180 SSP reactor at the end of the recycling process is decisive for decontamination. It restores the mechanical characteristics of the recycled PET and increases the intrinsic viscosity to the level of virgin material.
The PET recyclate is now food-safe and can be used for food packaging such as beverage bottles. More than 50 positive EFSA opinions, the US FDA as well as numerous brand owners in the food industry confirm the extraordinary decontamination results of the Starlinger iV+ process.
The installation of the 14 meters high Starlinger SSP reactor in an enclosure attached to the production hall at PET to PET’s recycling facility was captured on film: The spectacular scenes – partly shot from bird’s eye view with drones – can be watched in a video by clicking the following link: https://vimeo.com/502640873
PET-Recycling know-how from scratch
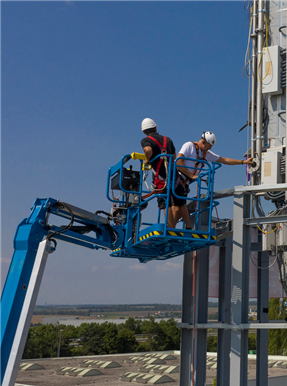
“Our customers all over the world appreciate the fact that we have been building up our know-how on PET and bottle-to-bottle recycling in-house for more than 25 years and continue expanding it based on our experiences”, says Paul Niedl, Head of Sales at Starlinger recycling technology.
“From extrusion to decontamination to refinement and here I mean food safety – of recycled PET we can provide substantial support to our customers in all areas.
Especially concerning food-grade regranulate there is no compromise: the safe and hazard-free packaging of our foods has highest priority.
The Starlinger decontamination process – which we also call super-cleaning process – creates a closed packaging loop where used PET bottles provide a valuable resource for safe and hygienic packaging.”
About PET to PET Recycling Österreich GmbH
With the PET recycling facility in Müllendorf the Austrian beverage industry meets the requirements of the Sustainability Agenda which was signed by the Austrian Federal Ministry of Agriculture, Forestry, Environment and Water Management, the Chamber of Economy, as well as representatives of the trade and waste industries. It aims, among other things, to establish targeted and ecological recycling of PET bottles in Austria.
The recycling facility is operated by PET to PET Recycling Österreich GmbH, in which Coca-Cola HBC Austria GmbH, Egger Getränke GmbH & Co. OG, Rauch Fruchtsäfte GmbH & Co. OG, S. Spitz GmbH and Vöslauer Mineralwasser GmbH hold shares.
At the PET to PET facility, the delivered PET bottles are screened and sorted by hand, and subsequently shredded and washed.
Then, the currently most modern processing methods are applied: On two separate processing lines PET flakes and PET re-granulate are produced, all in highest food-grade quality. Both types of recyclate are used in the production of new PET beverage bottles, depending on specific production requirements and aiming to achieve the highest possible share of recycled content.